Maintenance, Repair, and Operations (MRO) processes are essential for ensuring the functionality, safety, and longevity of facilities of all sizes.
MRO covers a broad range of activities, from routine upkeep and urgent repairs to managing the supply of critical operational tools and materials. Effective MRO practices minimize costly downtime, extend the lifespan of equipment, and protect both employees and assets.
A key, though often underappreciated, element of successful MRO management is accurate existing conditions documentation. Understanding a facility’s current state helps teams make quicker decisions, schedule maintenance efficiently, and mitigate operational risks.
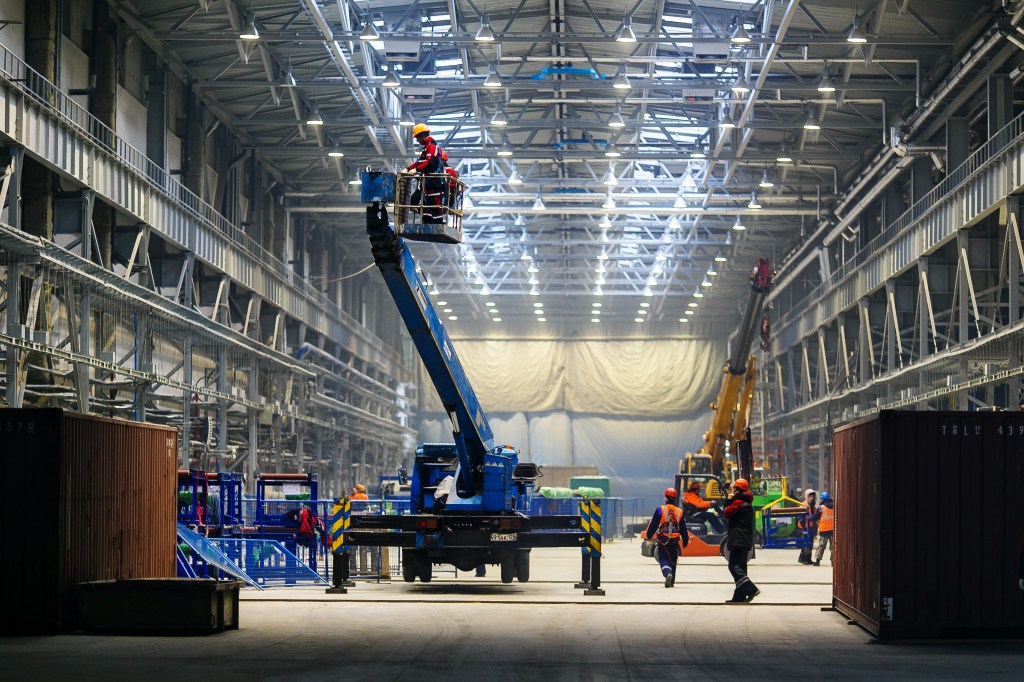
Efficient MRO practices prevent costly downtime, optimize equipment life cycles, and ensure the safety of employees and assets.
Key Components of MRO for Facilities
MRO includes several interconnected activities, all contributing to the operational sustainability of a facility. These activities fall into three primary categories:
1. Maintenance
- Routine tasks aimed at preventing equipment failure
- Examples: Lubricating machinery, replacing air filters, performing inspections
- Divided into:
- Preventive Maintenance: Regularly scheduled tasks (e.g., monthly or annually) to maintain equipment
- Predictive Maintenance: Uses data analytics, sensors, and monitoring to anticipate failures before they occur
2. Repair
- Unplanned fixes for equipment or systems that have malfunctioned
- Examples: Repairing a faulty HVAC unit, fixing wiring issues, patching roof leaks
- Goal: Minimize downtime by restoring systems to operational status as quickly as possible
3. Operations Support
- Tasks that ensure smooth facility operations, such as inventory management and energy monitoring
- Examples: Managing spare parts, overseeing environmental systems, following energy efficiency practices
Through these efforts, MRO ensures that facilities run efficiently, safely, and cost-effectively, reducing disruptions, enhancing reliability, and minimizing the need for costly reinvestments.
Challenges of Managing MRO for Complex Facilities
Managing MRO processes across large or complex facilities comes with significant challenges, often resulting from information gaps, poor documentation, or communication breakdowns among different teams. Key challenges include:
1. Inconsistent or Inaccurate Documentation
- Outdated or incomplete documentation makes it difficult to locate systems or troubleshoot issues.
- Example: Mismatches between floor plans and actual layouts of HVAC systems can delay repairs.
2. Unscheduled Downtime and Emergency Repairs
- Unexpected equipment failures force facilities to redirect resources at a higher cost.
- Without real-time infrastructure data, identifying and addressing root causes becomes more difficult.
3. Coordination and Communication Issues
- With multiple stakeholders—managers, technicians, contractors, and suppliers—involved, effective coordination is critical.
- Poor documentation slows communication, leading to resource mismanagement and delays.
4. Compliance and Safety Requirements
- Facilities must meet regulatory standards, and unplanned repairs can create compliance risks if not properly documented and tracked.
Accurate existing conditions documentation plays a critical role in addressing these challenges by enhancing communication, reducing downtime, and ensuring compliance.
What Is Existing Conditions Documentation?
Existing conditions documentation refers to detailed, up-to-date records of a facility’s physical state, including:
- Floor plans, blueprints, and schematics
- Diagrams of electrical, plumbing, and mechanical systems
- Asset inventories with equipment models, serial numbers, and specifications
- Assessments of structural elements such as windows, walls, and roofing
- 3D scans, digital twins, or photos of facility interiors and exteriors
This documentation is often generated using photogrammetry, laser scanning, or other advanced surveying methods. Facilities management platforms integrate this data with tools like CAFM or building information modeling (BIM) systems, providing teams with a centralized resource for updates and planning.
How Accurate Existing Conditions Documentation Enhances MRO
1. Speeds Up Repairs
- Clear schematics and system diagrams help technicians locate issues quickly and bring the right tools and parts
- Example: A technician fixing an HVAC issue can quickly identify control panels or ductwork locations, reducing downtime
2. Optimizes Preventive and Predictive Maintenance
- Access to equipment histories and inspection records helps managers predict when maintenance is needed
- Example: Knowing installation dates and specifications allows better scheduling of part replacements, minimizing disruptions
3. Improves Communication and Collaboration
- Shared documentation aligns contractors, engineers, and internal teams during repairs or upgrades
- Example: Using the same system layouts avoids confusion and streamlines collaboration on major projects
4. Reduces Operational Risks
- Up-to-date documentation helps identify potential hazards before they escalate
- Example: Proper records ensure that newly installed electrical panels are inspected and maintained to prevent fire hazards
5. Supports Inventory and Asset Management
- Accurate asset tracking allows teams to monitor equipment performance and ensure spare parts are available
- Example: A manager can proactively reorder parts before critical stock levels are reached, preventing delays
6. Ensures Compliance and Regulatory Readiness
- Complete records make it easier to demonstrate compliance during audits and inspections.
- Example: During an inspection, regulators can review documentation showing that the sprinkler system meets safety codes.

GPRS TruBuilt Existing Conditions As-Builts eliminate outdated and inaccurate as-builts and focus on real-time reality captured 2D CAD plan views that can integrate your infrastructure – above and below ground – to provide accurate existing conditions as-builts for your entire site or facility.
How GPRS Services Enhance MRO Efficiency
Effective MRO relies on having accurate information readily available. GPRS TruBuilt Existing Conditions As-Builts eliminate outdated or inaccurate documentation by providing real-time, precise 2D CAD plans that integrate both above-ground and underground infrastructure.
With TruBuilt as-builts, you can avoid project delays, minimize rework and change orders, prevent costly mistakes, and enhance safety by eliminating communication bottlenecks. Our SiteMap® platform (patent pending) allows you to access, copy, download, and share these plans seamlessly, keeping projects on schedule, within budget, and safe.
GPRS SiteMap® team members are currently scheduling live, personal SiteMap® demos.